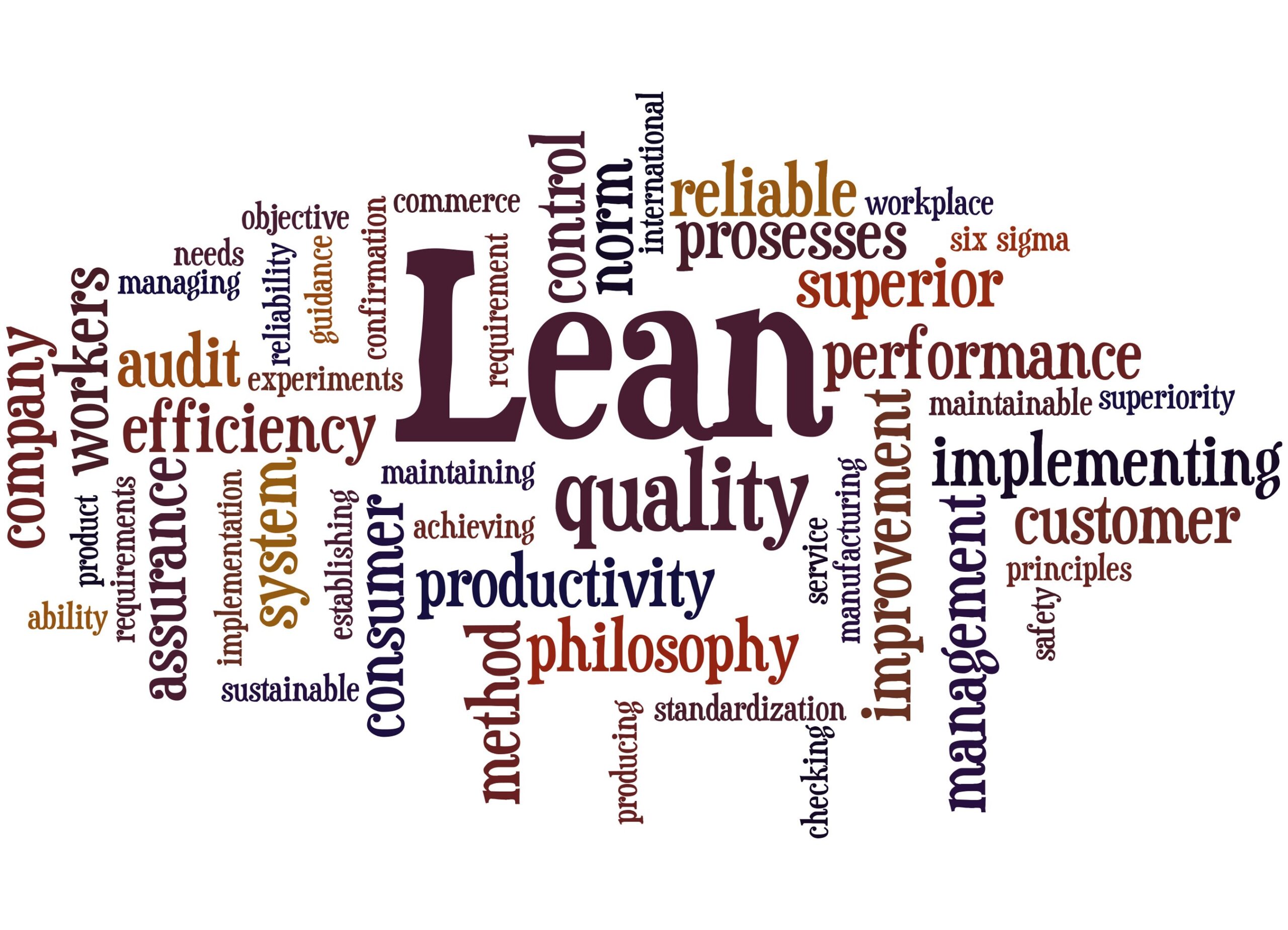
Boddingtons sets great store by its tradition of cross functional teams and continuous improvement work. The company’s LEAD based training is now into its second year and the pilot team recently presented some of its project work to the main board.
Boddingtons CEO Andy Tibbs said that ‘we were very impressed with both the qualitative and quantitive aspects of the presention. “To measure is to manage” – and our first cross functional team under the LEAD programme has already made measureable improvements in a number of manufacturing areas.’
Savings have been created through space economy, automation, cell redesign, work study analysis and other methods, freeing additional room at the company for manufacturing and adding existing value to projects. Tibbs says that ‘workplace innovations made for one customer inevitably knock-on to benefit many other parts of our manufacturing and many other customers. In that sense, our continuous improvement practices always benefit the whole company.’
Production manager Wayne Allen says that ‘at Boddingtons we are known for our daily morning disciplines of production monitoring and progress chasing. Investments and improvement have been made in our production briefing room. Having the extra LEAD teams now involved in the process gives an added charge to all our daily efforts.’
The message is clear – that workflow examination together with the acknowledgement of workflow achievements are both essential to good working practices, helping create a rising productivity curve at Boddingtons, Marden.